スクリュー式セントラル・エアコンのメンテナンスとセルフチェックのコツ
First, overhaul and maintenance project classification
(A) System maintenance:
1, air conditioner, fan coil maintenance; 2, air conditioning main unit maintenance;
3, terminal equipment maintenance service;
4, air conditioning cooling tower maintenance service.
- Cleaning:
1, refrigeration unit, cooling tower, hot and cold water system, air conditioning system, circulating water system;
2, heat exchange equipment, condenser, evaporator, cooling water system, refrigerant water system in the cold unit;
3, fan coil surface cooler, condensate pipeline equipment.
- Maintenance:
1, air conditioner, fan coil maintenance;
2, host system: compressor, vacuum valve, sight mirror, shield pump, real pump, heat transfer tube, condenser, evaporator, automatic control element;
3, cooling tower: fan, bearing, water distributor, filter, film material, tower parts, etc Two, maintenance cycle
- Daily repair and maintenance
time | position | Inspection items | correct 価値 |
Before startup | 1. Oil heater | Check if その エレクトリック heater is powered オン when stopping | Turn on the electric heater |
2. Oil separator sight glass | Check the oil level | Ensure that その オイル level is above 1/3 の その sight glass | |
Manual shut-off valve on the spray pipe | Check if the valve is fully open | Open the valve | |
4 Power Supply Voltage | Check with a voltmeter | Not exceeding ± 10% of the rated 価値 | |
5 Environmental 温度 (outdoor temperature) | Check the thermometer | ≤40℃ | |
Start up | Mirror covered on one side | Check the rotation of the star wheel | Connect according to EY302947 normally |
Electromagnetic valve on spray pipe 2 | Check if it is turned on at startup | ||
3 Vibration and noise | Feeling and listening | No abnormal vibration or noise | |
function | 1. Oil separator sight glass | Check the oil level | Supplement refrigeration oil* |
Mirror with two side covers | Check if there is fuel injection | ||
3 Exhaust 圧力 | Check the high-pressure gauge (exhaust) | 1.1~1.8MPa | |
4. Inhalation 圧力 | Check the low pressure gauge (suction) | 0.30.6MPa | |
5 suction pressure difference | Check the low pressure gauge (suction) | ≤0.05MPa | |
1. Hot water outlet 温度 (during heating) | Check the thermometer | 30~45℃ | |
2. Temperature の chilled water outlet (during refrigeration) | Check the thermometer | 5~10℃ | |
3. High and low pressure difference | Check the high-pressure gauge (exhaust) | 0.1MPa | |
Every season | 1. Refrigerant injection amount | Check the liquid microscope | Pipeline liquid without bubbles |
2. Lubricating oil injection amount | Check the oil level gauge | Within the prescribed scope |
- body maintenance cycle
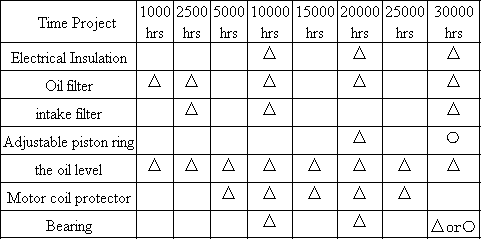
Note: △ Inspection or cleaning, ○ replacement According to the maintenance cycle of the above table, when it is necessary to replace the air conditioning piston ring or bearing, it should be implemented by the technical personnel approved by the compressor manufacturer or sent by the compressor manufacturer to assist the service.
Three, maintenance key projects
- Power supply and control part
1, the working power supply of the unit is 3N~, AC380V, 50Hz. Need to check the electric control cabinet in the power supply part and control part of the abnormal and fixed terminals, including the total power wiring copper bar, automatic air circuit breaker (air switch), δ-δor Y-δcompressor start electrical device, PLC touch screen, target flow switch, freezing, cooling water pump linkage control line (control contact for passive contact), temperature sensor, freezing, cooling water pump, Cooling tower linkage control line (control contact is passive contact), electronic control instrument and so on nodes.
2, check the power supply voltage: the maximum allowable phase voltage imbalance is 2%, and the phase current imbalance is 10%. Phase voltage imbalance is greater than 2%, absolutely can not be turned on.
For example: the nominal voltage is 3N~, AC380V, 50Hz, measured UAB=376V, UAC=379V, UBC=385V. Get the average voltage = (376+379+385) /3= 380V: Determine the deviation from the average voltage:
△UAB=380-376=4V, △UAC=380-379=1V, △UBC=385-380=5V, the maximum deviation value is 5V, 5/380=1.3%, the maximum phase voltage unbalance is 1.3%.
Please inform the user that the damage caused by startup operation when the phase voltage unbalance is greater than 2% is regarded as improper operation and is not covered by the warranty of this product.
- Operation and appearance of the system (leakage, damage)
- Confirm that the system is not leaked.
- Check that the sequence of actions is normal.
3, check whether the compressor wiring is correct or loose.
4. Measure whether the working current of each compressor is normal.
5, check whether it is correctly installed, and confirm that the flow switch and the control cabinet have been correctly connected.
6, point chilled water, cooling water pump and cooling tower fan, check the motor phase sequence.
7. Check whether the coil of the compressor capacitive solenoid valve is locked, and whether the capacitive capillary is damaged.
8, check the water side of the pressure gauge and thermometer connection is correct, flow switch is normal.
9, check whether the oil level in the compressor is normal, the normal compressor oil level is generally in the middle of the sight mirror.
10, all the system (condenser outlet Angle valve, compressor suction, exhaust stop valve, etc.) in the open state.
11. Check whether the high and low pressure Settings of the pressure relay are normal (high pressure is set to 1.8MPa, low pressure 0.2MPa).
12, check whether the cooling tower/expansion tank water supply device is smooth, whether the automatic exhaust valve can automatically exhaust.
13, confirm whether the unit has abnormal noise. There is no contact, collision or friction between pipes and pipes to protect and clean.
14, check the frame and other metal shell such as rust, with coarse sandpaper and cloth to wipe rust spots apply anti-rust paint.
15, adjust the water flow and check whether the water pressure drop through the evaporator and condenser meets the requirements of the normal operation of the unit. That is, the inlet and outlet pressure of the chilled water and the inlet and outlet pressure of the cooling water of the unit should be guaranteed at least 0.2MPa
- The use of lubricating oil specifications and precautions
1, lubricating oil with lubrication, cooling, sealing, driving hydraulic cylinder and other functions. It has a decisive impact on the performance of the screw compressor, if used improperly or incorrectly, it will lead to serious damage to the compressor body. Therefore, the internal lubricating oil system is the key to the normal operation of the compressor, but the performance of the oil changes with time, and there is a relatively stable period of time when the performance will be sharply deteriorated. Therefore, the oil should be changed at the right time.
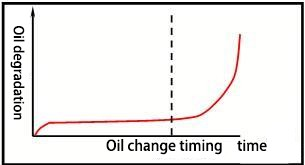
2, when should replace the lubricating oil to ensure the normal operation of the compressor, can be in accordance with the following methods:
- Time set replacement: generally every 10,000 hours to check or replace the lubricating oil, and after the first operation, the air cooling and dry unit with screw compressor 1000 hours recommended to replace the lubricating oil and clean the oil filter. Because the residue of the system assembly will accumulate to the compressor after the formal operation. Therefore, for air-cooled and dry units with screw compressors 1000 hours (cumulative 2 months) should be replaced once, and then according to the cleanliness of the system to replace regularly, if the cleanliness of the system is good, you can replace once every 10,000 hours (or annually).
- If the exhaust temperature of the compressor is maintained at high temperature and high pressure for a long time, the deterioration of the lubricating oil is accelerated. It is necessary to check the chemical characteristics of the lubricating oil regularly (every 2 months), and replace it when it is unqualified. If it can not be checked regularly, it can be performed according to the following suggestion table.
The operation period is based on 16 hours of operation per day
running state | refrigeration | Heating at 45 ℃ | Heating at 50 ℃ | Heating at 55 ℃ | Heating above 55 ℃ |
Replacement time (hours) | 10000 | 8000 | 4000 | 1500 | 500 |
Replacement time (number の operating months) | 20 | 16 | 8 | 3 | 1 |
3, the acidification of lubricating oil, will directly affect the life of the compressor motor, so it should be regularly checked whether the acidity of lubricating oil is qualified, the general acidity of lubricating oil below PH6 must be replaced. If the acidity can not be checked, the dryer filter element of the system should be replaced regularly, so that the dryness of the system is maintained in a dry state.
4. The replacement procedure of lubricating oil needs to consult the compressor manufacturer after sale. In particular, the system has a motor burn precedent, after replacing the motor, it should track the lubricating oil condition every month, or replace the lubricating oil regularly (200 hours), until the system is clean, otherwise the residual acidic components in the system will destroy the motor insulation.
User's notice: Each manufacturer's compressor lubricating oil brand is different, please pay attention to the lubricating oil brand and dosage indicated on the original compressor nameplate when replacing the lubricating oil. Special attention: Because different types of lubricating oil contain anti-rust, anti-oxidation, anti-foam, anti-abrasion and other components are different, do not mix different types and different brands of oil, so as to avoid chemical reaction. Sticky deposits can clog the oil system. If the user replaces it privately, it shall be regarded as improper operation and not covered by the warranty of the product.
(4) Water quality management of circulating water (chilled water, cooling water)
The poor water quality of chilled water and cooling water will not only scale in the heat transfer pipe, affect the heat exchange efficiency, reduce the performance of the unit, but also corrode the heat transfer pipe resulting in major failures of the unit. Customers should be in accordance with the requirements of GB50050-1995 "Industrial circulating cooling water treatment design code" for water quality treatment. When the chilled water system is a closed system, soft water should be used. The cooling water (chilled
water of the open system) should be sampled and analyzed regularly during the operation of the unit, and the water quality should meet the requirements of Table 3-3. If it does not meet the requirements, water quality treatment should be carried out.
User notice: due to water untreated or improper treatment caused by corrosion, erosion or unit performance decline;
Four, maintenance methods and steps
(1) Oil change and filter dryer (must)
1. Preparation: Check whether the compressor lubricating oil is preheated for more than 8 hours. Before the test run, the oil heater should be energized for at least 8 hours to prevent frothing of frozen oil when starting. If the ambient temperature is low, the oil heating time needs to be relatively longer. When starting at low temperature, due to the large viscosity of lubricating oil, it will be difficult to start and the compressor will not be able to load and unload. Generally, the minimum temperature of the lubricating oil needs to reach 23℃ or more before it can be operated, started, started, recorded operating parameters to analyze the problems existing before and now. Make good preparations.
Short-circuit the high-low differential switch (Figure 1). (It is best not to adjust the differential pressure switch, and the two wires can be short-connected directly.) Run the machine at full load (100%). Close the corner valve (Figure 2). (Pay special attention to restore differential pressure switch after refrigerant recovery)
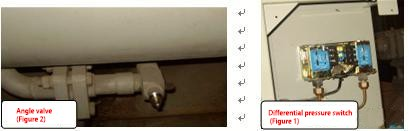
- Press the emergency switch or turn off the power when the low pressure pressure of the machine is less than 0.1MP. Since there is a check valve at the exhaust port of the compressor (Figure 1), the refrigerant will not return to the press, but sometimes the check valve may be closed loosely, so it isbest to close the stop valve of the press exhaust while pressing the emergency switch (Figure 3).
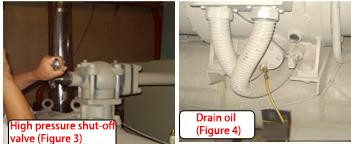
2, when the above work is completed, turn off the main power supply. Carry on the following process
- Oil, frozen oil in the system under the pressure of refrigerant gas spray speed quickly pay attention to health do not spray
Splash to the outside. Drain refrigerant while draining oil, open high pressure gauge stop valve (Figure 4)
- Clean the oil tank and oil filter (Figure 5) Open the cover of the oil tank and clean the dirty oil tank gauze with dry gauze. Then pour the spent frozen oil into the fine gauze. Remove the two magnets in the oil tank and clean them before putting them back into the oil tank. Use a big wrench to disassemble the oil filter and clean it with waste oil.
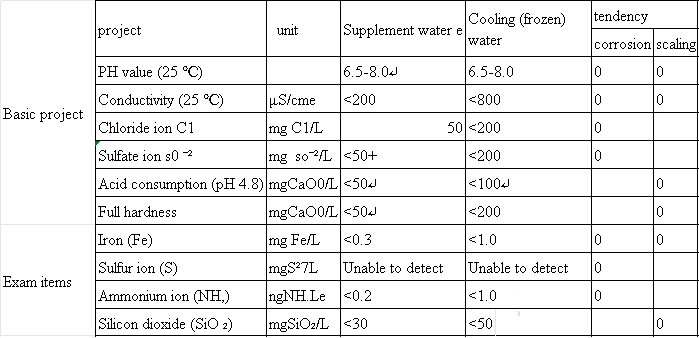
Replace the refrigerant filter A, the refrigerant filter core has 3 in the replacement speed should be fast, to prevent too long contact time with the air adsorption of too much water. B, the filter is packaged in cans, pay attention to protection during transportation, once the packaging is damaged, it is scrapped.
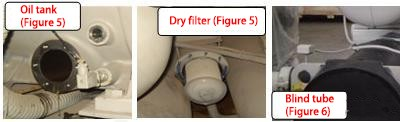
3, vacuum refueling according to the compressor structure is best from the high pressure side of the refueling. Because the high pressure and low pressure chamber of the compressor are not directly connected, it is difficult to return to the oil tank from the low pressure refueling. Generally, we use the way of vacuuming to evacuate the oil from the low pressure side and inhale the oil from the high pressure side.
About vacuuming. The purpose is to pump out the moisture and air in the system. When the vacuum pump is sealed or aging is more serious, the vacuum degree can not meet the requirements, then it is useless to evacuate such a vacuum pump for a long time)
About 真空 damage. When evacuated to the negative pressure, open the Angle valve to release a little refrigerant from the condenser, which will destroy the vacuum of the system
Note: Liquid supply solenoid valve, because the solenoid valve is also closed when the machine is closed, so when the refrigerant oil is added, the pressure difference switch is restored. Turn on the power to preheat and power on the solenoid valve (can be connected to the oil heater)
Fill the blind tube with oil: fill the blind tube with oil after filtering the replaced old refrigerant oil.
4, preheating: power on preheating at least the oil heating to 23℃ or more to run the boot operation.
- Open the condenser to clean, clean the system of debris, welding slag, dust, some anti-rust coating and so on.
General high pressure pressure corresponding to the saturation temperature condenser outlet water
temperature, when the temperature difference is greater than 3--5 degrees need to clean the condenser. We do not recommend frequent chemical cleaning of the condenser to prevent corrosion of the condenser perforation leakage of fluorine, so it is very important to keep the circulating water clean and softened.
However, when the condenser must be cleaned, a professional water treatment expert should be found for analysis.
- Unit parameter setting
1. The chilled water temperature is generally set at 7 degrees. (Anti-freezing protection is set to 4 degrees, when the weather is cool and the indoor load is too low, the water temperature may drop too fast and the machine has no time to stop the anti-freezing protection, then the water temperature can be set to 9 degrees).
2, summer indoor load is too high when the boot may appear compressor overload failure. (At this time, the refrigerated pump should be turned off to reduce the water flow, and the water valve should be fully opened when the water temperature is below 15 degrees. Prevent high pressure or overload failure due to excessive load and low pressure for a long time).
3, the cooling water temperature is best not higher than 40 degrees can not be lower than 25 degrees. (When the weather is cool, the cooling water valve can be turned off to keep the cooling water above 25 degrees)
4. Machine operation data must be recorded. Before starting, should check the power supply voltage phase imbalance can not be greater than 2%. When the pressure is less than 5kg, it is not allowed to start, and then the machine may leak fluorine to prevent the system water from burning the compressor when it is started.
Five, common troubleshooting
- Solenoid valve failure
Fault phenomenon | reason | Trouble shooting |
Closing action time exceeds 3 seconds | The small hole on the side of the valve plug is blocked | Eliminate dirt inside その small hole そして install a filter で front of the valve |
The valve does not open after the power is turned オン | 1. The power supply voltage is below 85% | Adjust the power supply voltage within ± 10% range |
Coil burnt out or connector detached | If necessary, use a manual device to open the valve for maintenance or replace the coil. The newly wound coil must be soaked そして dried, そしてa layer の quartz powder and asphalt (weight to weight ratio 3:1) composite adhesive should be soaked between その coil そして その shell | |
The gap between その valve plug そして その valve seat is not sealed, and there is leakage | The small pores オン その side の その valve plug are blocked, making it difficult to transmit medium pressure | Eliminate dirt from small holes |
The seal on the valve plug is damaged, worn or deformed | Replace the sealing ring | |
The pressure difference between the front and rear of その valve is less よりも 10% の その standard 圧力 価値 | Comply と その regulations オン その front そして rear pressure difference in the product manual | |
The static そして dynamic sealingpoints の その valve body are not sealed | The sealing gasket is not placed correctly | Place その sealing gasket correctly そして tighten it evenly そして reliably |
Sealing gasket deformation, wear or decay | Replace the seal | |
The valve plug does not start after being powered オン | There is dirt inside the pressure relief hole | Eliminate dirt inside the pressure relief hole |
Inappropriate control medium, i.e. viscosity too low | The viscosity の その medium is low, そして その 圧力 relief hole should be appropriately increased |
- The compressor is faulty
Fault phenomenon | reason | Troubleshooting |
The compressor cannot start | The main switch failed to close | Close the switch |
The fuse is blown そして その circuit switch is not closed | Check whether the circuit and motor winding are short circuited または grounded, whether there is overload (after troubleshooting), replace the fuse or close the switch, and check whether the connection is loose or corroded | |
Thermal overload protection disconnected | Overload protection automatically resets, そして その fault is eliminated before その サーマル overload protection is restored to safety | |
Contactor or electromagnetic coil malfunction | Repair or replace | |
Shutdown due to safety device protection | Determine その タイプ そして cause の その shutdown, そして troubleshoot the issue before restoring the safety switch | |
No heat load | Waiting for heat load | |
Repair or replace the electromagnetic coil | ||
Check if その motor has any open circuit, short circuit or burnt out | ||
Check all wire connectors そして tighten その wire terminal bolts | ||
Reset the safety switch | ||
The compressor cannot operate but makes noise | Wiring error | Check and rewire |
Low Voltage | Check the power supply voltage | |
Starter failure | replace | |
Compressor damage | replace | |
The compressor has abnormal noise and vibration | A large amount の refrigerant enters その compressor | Check the setting of the expansion valve |
Compressor damage | replace | |
The compressor cannot increase or decrease the load | Energy control malfunction | replace |
The load shedding device has malfunctioned | replace | |
Temperature controller level malfunction または wire disconnection | replace | |
Unreasonable level setting | RESET | |
The interval between increasing そして decreasing その load of the compressor is too short | Abnormal water temperature controller | replace |
Insufficient water flow | Adjust water flow rate | |
Compressor thermal protection switch disconnected | Operating conditions exceed the design range | Improve conditions to keep operating conditions within acceptable limits |
The exhaust valve is not fully open | Open the valve | |
motor fault | Replace the compressor |
- The motor overload relay is disconnected
Reason | Troubleshooting |
Voltage too low under high load conditions | Check if the voltage drop of the power supply is too large |
Motor winding damage | Replace the compressor |
Loose power cord | Check all connections and tighten them tightly |
The condensation temperature is too high | Refer to the method for handling high exhaust 圧力 |
Voltage imbalance caused by power line failure | Check その power supply voltage, notify その power supply bureau, そして do not start その compressor until その fault is resolved |
Overload relay broken, high ambient 温度 | Improve ventilation to increase heat dissipation |
- The unit is faulty
Fault phenomenon | reason | Troubleshooting |
Exhaust pressure too high | There are non condensable gases in the system | Discharge non condensable gases |
Excessive refrigerant charge | Extract excess refrigerant | |
The exhaust shut-off valve is not open | Open the exhaust shut-off valve | |
The outlet temperature of the condenser is too high | Check if the installation of the unit is appropriate and if the fins are scaled | |
Exhaust pressure too low | Improper adjustment of condensation 温度 | Check the control and operation process of the コンデンサー |
The suction shut-off valve is not fully open | Open the suction shut-off valve | |
Insufficient refrigerant | Leak detection, repair and refrigerant filling | |
Low suction 圧力 | Refer to the correct steps for handling low suction pressure below | |
Refer to the following methods for handling compressor overload failure | ||
Abnormal fuel supply | Oil filter inlet blockage | clean |
Liquid refrigerant enters the oil fraction | Check その エレクトリック heater, adjust その expansion valve to increase superheat, check the liquid supply solenoid valve, and adjust the water flow rate | |
The oil pressure gauge is inaccurate | Repair or replace, close the valve and only open it when there is a reading | |
Low oil level | come オン |
終了!